Grinding of construction materials with an angle grinder.
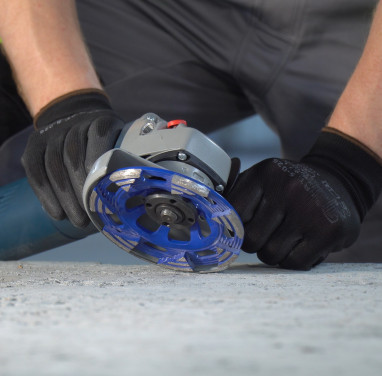
During renovation work, it is often necessary to grind various surfaces for further processing or cladding. Grinding construction materials, both indoors and outdoors, is considered rough work since these surfaces will later be covered with finishing materials.
Most often, this is a rather labor-intensive process that puts a load on the equipment, the operator's hands, and sometimes even the back. To perform such work as comfortably and quickly as possible, it is important to carefully choose both the equipment and the consumables. Special milling cutters with diamond segments are used for this type of work.
In this article, we will tell you everything about grinding construction materials with an angle grinder, as it is the most common and affordable tool for grinding. However, when it comes to large-scale work, this equipment is significantly inferior to industrial grinding machines.
Choosing an angle grinder for grinding.
The most common type of angle grinder for grinding is the 125 mm model. However, craftsmen often use more massive angle grinders (150, 180, or 230 mm) together with a 125 mm milling cutter, as their weight helps stabilize the cutter during operation and significantly reduces the load on the operator's hands.
Since 125 mm cutters and grinders are the most popular, we will focus on them. What parameters should you consider when choosing an angle grinder?
Power. Low-power grinders are not suitable for grinding construction materials, as the process puts a heavy load on the drive, making them inefficient. The minimum recommended power for a 125 mm angle grinder is 1.2 kW, with the optimal range being 1.4 kW or higher. The higher the power, the faster the process and the longer the consumables last.
Power supply. Battery-powered grinders are not recommended because they usually have lower RPMs compared to corded models. They also lack sufficient power, and during prolonged work, batteries discharge quickly, slowing down the entire process due to frequent recharging. Therefore, corded angle grinders are the best choice.
RPM. Grinding is almost always performed at maximum speed, so it’s best to choose equipment with RPMs of at least 11,000. Variable speed is not a must, as it is rarely used — mainly for specific materials.
Manufacturer. Since grinding puts a lot of strain on the grinder’s drive, it’s not advisable to use cheap Chinese brands, as they will fail quickly. It is better to invest in a high-quality, reputable brand — the tool will last much longer and save you money in the long run.
Once the angle grinder is properly selected for grinding construction materials, we can take a closer look at the main grinding operations.
Main operations
There are not many main operations in grinding construction materials since most work is usually done by cutting.
Removing excess concrete after formwork. After dismantling the formwork from various surfaces (walls, ceilings, stairs, etc.), concrete build-ups can often be found in certain areas, which are difficult or even impossible to cut off. Grinding is used for such tasks.
Leveling concrete floors. Whether it’s a newly poured floor or an old one with defects, it’s rarely perfectly level. Grinding is the only effective method for leveling such surfaces.
Grinding door and window openings. It’s very difficult to cut openings exactly to size. Therefore, grinding is often used to adjust openings to the required dimensions.
Removing paint or coatings. Various surfaces may have paint or coatings that need to be removed, either to apply a new layer or to prepare the surface for tiling.
Artistic grinding. This is a specialized type of work requiring a high-quality surface finish. Artistic grinding often involves a wide range of materials, so it’s better to use an angle grinder with variable speed control and choose specialized cutters for this kind of task.
Often, all these operations are performed on concrete, but other materials with different physical properties may also be encountered, requiring different processing approaches.
Materials and Their Workability
In addition to concrete, which itself can vary in composition and behavior, other materials may also be involved — and each requires a specific approach.
For example, fresh screed is highly abrasive and quickly wears down the segments, while old, high-grade concrete is extremely hard, has very low abrasiveness, and is slow to process. Two key parameters — hardness and abrasiveness — directly influence how the material is processed, and they are inversely related.
The higher the material's abrasiveness, the lower its hardness, and vice versa. All construction materials, in terms of workability, can be conditionally divided into three categories: highly abrasive, medium abrasive, and low abrasive.
On one axis, the frequency of use shows how often a particular material is used in construction, while the other axis represents the abrasiveness of various materials as a percentage. Most often, materials with an abrasiveness ranging from 40% to 80% are subjected to grinding.
Knowing which material we will be working with on-site and the scope of work allows us to move on to the next stage — selecting the diamond consumable for grinding.
How to choose the right milling cutter for the material and work volume?
The first thing to consider when choosing a consumable is the tool's lifespan and grinding speed. Let's take a look at the positioning table that shows these parameters using all milling cutters from the "Distar" brand as an example.
As we can see from the table, the fastest milling cutter has the shortest lifespan, while the most durable one offers almost the lowest processing speed. An important factor when selecting a cutter is its weight.
It’s one thing when we are grinding a floor and transferring the weight of the angle grinder and cutter onto the material, and quite another when grinding a ceiling or working overhead with outstretched arms.
The weight of the cutter affects not only the operator's fatigue but also the tool's lifespan and working comfort. Excessive weight or imbalance significantly increases the gyroscopic effect during operation, placing additional load on the drive.
As you can see, the weight of the milling cutters can differ by more than 60%, which significantly affects operator fatigue when working at heights or with outstretched arms. Now, let’s take a closer look at the advantages of each cutter.
Expert. Since this cutter is the heaviest, it is most suitable for floor grinding. It also has a large diamond segment area, providing good flatness of the processed surface. Additionally, this cup wheel is the most budget-friendly option in the "Distar" range.
Rotex. This cutter has an interesting boomerang-shaped segment design and is equipped with additional holes to reduce weight and improve dust extraction when working with low-power vacuum cleaners.
Raptor. The lightest cutter, ideal for processing any surfaces, including overhead work or working with outstretched arms. In addition to its minimal weight, it offers high performance, significantly reducing operator fatigue as tasks in hard-to-reach places are completed much faster.
Beton Pro and Beton Uni. These cutters from the "Baumesser" range are the cheapest of all listed. They have relatively low durability and are best suited for small-scale tasks.
When the task is to grind relatively small objects, instead of buying an expensive and long-lasting cutter, you can choose one of these options.
Now, knowing the tasks on-site, you can easily decide which cutter will perform them comfortably, quickly, and cost-effectively — though it’s not always possible to combine all three.
Working with a vacuum cleaner
Among all types of diamond processing of construction materials, grinding produces the largest amount of dust.
This can be kilograms or even tens of kilograms of heavy airborne dust, which not only affects the respiratory system but also reduces visibility when working indoors, thus slowing down the work process.
Therefore, for comfortable and more productive work, vacuum cleaners and special dust extraction attachments for grinding are used.
The most effective dust extraction is provided by cutters like Raptor and Rotex, as they have additional holes in the body that improve dust removal efficiency, even when working with relatively low-powered vacuums.
By using these cutters, you make the grinding process cleaner, more comfortable, and faster!
Low performance during grinding. How to sharpen diamond cutters?
When working with low-abrasive materials, diamond grains can become glazed, significantly reducing processing speed.
This doesn’t mean the cutter is worn out or of poor quality — the diamond edges simply need to be exposed, and the cutting ability will be restored, noticeably increasing the processing speed.
To effectively open up the diamond cutter, work it briefly on highly abrasive materials — such as aerated concrete, foam concrete, abrasive sandstone, fresh concrete, or asphalt.
Conclusions
In summary, for comfortable grinding of construction materials, you need a powerful angle grinder with high RPM and several cutters suited for different tasks and volumes of work.
For better comfort and cleanliness, it’s recommended to use dust extraction. Properly selected consumables will significantly increase work speed, reduce costs, and ease the load on both the operator and the power tool!