Dry drilling of construction materials. Q&A.
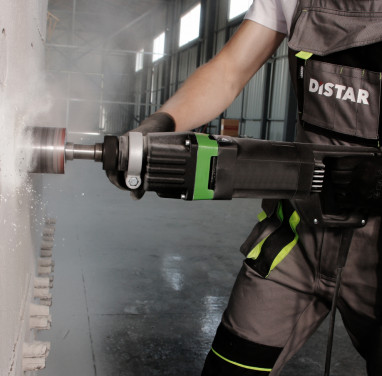
Dry drilling is mainly performed in areas where water cooling is not allowed or possible. Sooner or later, many professionals encounter such projects and begin to explore this topic in detail.
Naturally, questions arise — how to choose the right equipment, which consumables to use, and what problems one might face during this type of work. This is exactly what we’d like to discuss.
Equipment for Dry Drilling
One of the most important aspects is selecting the right equipment. If you simply need to install a few extra sockets at home, there’s no need to invest in expensive power tools. However, if your goal is to make a living installing air conditioners or electrical outlets, then it’s definitely worth purchasing more expensive, professional-grade equipment.
Let’s take a look at the types of equipment available along with their main advantages and disadvantages.
Equipment | Disadvantages | Advantages |
---|---|---|
Rotary Hammer | Low RPM, low power, small drill diameters, average drilling speed | Affordable price, ability to work with carbide core bits |
Impact Drill | Low RPM, low power, small drill diameters, average drilling speed | Affordable price |
Diamond Core Drilling Machine (DDM) | Medium price | High RPM, multiple speed settings, high power, medium and large drill diameters (when using a stand) |
DDM with Micro-Impact Function | High price, requires special core bits designed for micro-impact | High RPM, multiple speed settings, high power, micro-impact function, highest drilling speed, medium and large diameters (with stand) |
The key difference is that drilling a socket hole in the same concrete with a rotary hammer can take 4–5 minutes, while using a diamond core drilling machine with micro-impact takes just 1 minute.
And when it comes to large volumes of work, the more expensive equipment will save us a significant amount of time. Based on our needs and budget, we can choose the right power tool and move on to the next stage — selecting the drill bit.
Types of Consumables
The choice here is not very wide, as there are only two types of core bits — carbide and diamond. Carbide core bits are used only with rotary hammers in hammer + drilling mode. This is the cheapest drilling method but also the slowest.
Holes made this way are usually quite rough, unlike those drilled with diamond core bits. Finishing such holes can take much more time than if we used diamond consumables from the start.
Diamond core bits can be used with any equipment, but only in non-impact mode (the exception is micro-impact).
At first glance, the choice may seem simple since there are only two main types of bits on the market. However, there is a huge variety of diamond core bits designed for different materials and equipment. Here’s what you should pay attention to when choosing your consumables:
- Recommended equipment
- Arbor size or the presence of an adapter for your existing equipment
- Range of materials the bit is designed to drill
- Optimal RPM range for the bit
- Manufacturer’s stated lifespan
Now we have the minimum required set to start working, so it’s time to dive into the drilling process itself.
Main Operations
When arriving at the job site, the specialist may face various tasks, each requiring specific diameters of consumables. The drill bit diameter and length are selected based on the task.
- Electrical socket installation – the most common core bit diameters for drilling socket holes are 68 mm and 72 mm. For junction boxes, a diameter of 82 mm is used.
- Ventilation – diameters range from 102 mm to 132 mm.
- Air conditioner installation – 52 mm to 62 mm.
- Heat recovery system (HRV/ERV) – 82 mm to 132 mm.
- Sewer system – 112 mm to 132 mm.
- Gas pipeline – 32 mm to 42 mm.
- Extractor hood / Exhaust – 112 mm to 122 mm.
Based on this data, we understand that to perform all possible drilling tasks in apartments, it is necessary to have a wide range of core bit diameters from 52 mm to 132 mm in your arsenal.
A very important point — all power tool manufacturers clearly specify the maximum drill bit diameter allowed for use in dry mode during handheld drilling. Most often, the maximum hole diameter allowed for handheld work is 82 mm, and anything larger requires the use of a stand.
At the same time, one crucial factor is the material being drilled. If the material has low strength and high abrasiveness, manual drilling with large diameters is acceptable. Some specialists even manage to drill manually with 200 mm bits or larger!
Materials We Encounter During Drilling
Construction materials vary greatly in terms of hardness and abrasiveness.
Abrasiveness refers to the material's ability to sharpen the diamond edges during drilling, increasing speed and preventing the diamond segment from glazing. Abrasive materials are low in strength and therefore easy to process. However, they wear down the diamond layer much faster than harder materials.
So, what materials might we encounter on the job site?
- Plaster
- Cinder block
- Silicate brick
- Aerated concrete
- Brick
- Abrasive concrete
- Concrete
- Reinforced concrete
Each of these materials has a different level of hardness and abrasiveness, which means they will all affect the drill bit’s lifespan and drilling speed differently.
Concrete is the hardest and least abrasive material, making it the most challenging to drill.
Factors Affecting Concrete Drilling Speed
While working with this material in different locations, you may notice that the same drill bit and equipment deliver completely different drilling speeds and tool life. What factors can influence the physics of this process?
- Concrete grade
- Age of the concrete
- Presence of metal reinforcement in the structure
- Aggregate size (fraction) used in the concrete mix
- Moisture content of the material
- Availability or absence of dust extraction
All these factors directly or indirectly affect drilling speed and the lifespan of consumables. Some drill bits are not recommended at all for high-strength concrete or when working with reinforced concrete, while others are specifically worth purchasing only if you are working with dense, heavily reinforced, high-grade concrete.
Common Drilling Problems and Solutions
Does any job ever go completely smoothly? Of course not! Concrete drilling is no exception — various challenges and problems can arise. It’s important to be prepared and know how to solve them.
Starting the drill in the material. The initial contact of the drill bit with dense material is quite harsh, and drilling into it "right away" without enough experience can be very difficult. If the hole location is strictly marked and there’s no room for error, even 1 cm, starting freehand is almost impossible. Solution: Use templates or centering guides to ensure precision.
Working at a site where dust is not allowed. Did you know that even drilling a simple socket hole produces about one glass of dust, most of which spreads around the entire room?
What if the drilling is done in a freshly renovated room where dust is unacceptable?
Solution: Special tools from "Mechanic" designed for dust extraction during dry drilling will help solve this problem.
And, of course, a vacuum cleaner is necessary to perform such work cleanly.
The drill bit sparks and barely progresses. Most likely, you’ve hit metal (rebar, steel channel, etc.). The cutting process is completely different when drilling metal — it’s much slower than concrete. Solution: Assess how much metal is in the drilling path. If it’s a large steel channel and you have the option to shift the hole — it’s better to do so. If not — continue drilling, but make sure to pause periodically to let the drill cool down and avoid damaging the cutting edges.
The tool stops drilling completely. If the concrete has a high gravel content, the diamonds in the drill bit can glaze over, resulting in a complete loss of cutting ability. Solution: "Open" the segments by drilling into abrasive material such as brick or asphalt to restore the bit’s performance.
The drill bit isn’t long enough to drill through the wall. If your bit is too short to complete the through-hole: Solution: Use a special extension adapter. After removing the core from the hole, attach the extension between the bit and the power tool and continue drilling.
You might face other problems during work, and you’ll figure out your own solutions as you gain experience.
Over time, you’ll quickly learn to assess how tough the concrete is on each site, and based on the material, select the right drill bit and equipment.
By choosing high-quality tools and consumables, your work will become much more comfortable and efficient, and your equipment will serve you much longer!