Diamond cutting with millimeter precision: how to choose an angle grinder and blade for any task
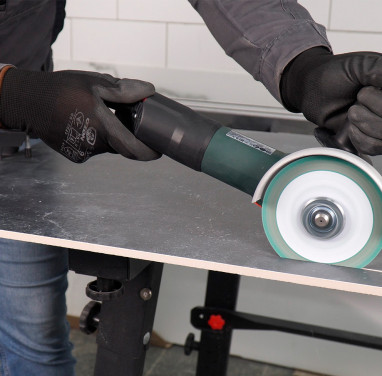
An angle grinder (AG) is one of the most versatile tools on a construction site, during renovation, and finishing work. Thanks to a diamond blade, even a compact "grinder" becomes a high-precision cutter capable of working with concrete, brick, tile, granite, marble, metal, and other construction materials.
In this article, we will explain in detail how to properly select an angle grinder and diamond blade for a specific task, what to pay attention to when choosing, and which types of work each tool is best suited for.
How to choose an angle grinder
The choice of angle grinder directly affects productivity, cut quality, and safety. Important: effective work requires not only high-quality consumables but also appropriate electrical equipment.
Let’s look at the key parameters.
Disc diameter
Common AG disc sizes:
-
75 mm – precise cuts for flush buttons, hatches, sockets, etc.
-
115 mm – for small and accurate cuts
-
125 mm – the most popular diameter (cutting depth up to 35 mm)
-
150 and 180 mm – intermediate options
-
230 mm – for deep cuts (up to 65 mm)
The larger the disc, the more powerful the equipment must be: petrol cutters, joint cutters, or wall saws.
Power of the equipment
To work effectively with hard materials, the angle grinder must have sufficient power:
-
for a 125 mm disc – from 1.5 to 1.7 kW
-
for a 230 mm disc – from 2.2 to 2.7 kW
The denser the material, the more important the power reserve. A powerful motor also maintains stable RPMs, which is critical when working with diamond tools.
Rotation speed
To achieve optimal linear speed (80 m/s):
-
AG with 125 mm disc – about 11,000 rpm
-
AG with 230 mm disc – about 6,500 rpm
Failure to meet these parameters can lead to overheating, blade damage, or reduced cutting performance.
Main types of work with an angle grinder
Diamond cutting can be roughly divided into two types:
-
Rough cutting – when edge appearance is not important:
-
openings for doors, windows
-
wall chasing for utilities
-
dismantling hidden structures
-
processing blocks and bricks
-
-
Fine cutting – when accuracy and neatness matter:
-
trimming paving stones, curbs
-
cutting tiles, marble, porcelain
-
trimming facade materials
-
creating decorative elements
-
Tip: for rough work, affordable blades can be used. Fine cutting requires high-precision tools with minimal chipping.
Abrasiveness and hardness of materials
Abrasiveness – the material's ability to wear down the diamond layer.
Hardness – resistance to destruction. The harder the material, the lower its abrasiveness, and vice versa.
Most construction materials (excluding metals) are conventionally divided into three groups:
-
Low hardness / high abrasiveness
Aerated concrete, silicate and ceramic brick, gas concrete, cement screed, fresh concrete, asphalt.
Recommended wear-resistant blades:-
Stayer – for asphalt
-
Beton Pro, Bestseller Universal, Ziegelstein – for brick and gas concrete
-
Razem, Keramik – for rough tile cuts
-
Esthete, Perfect – for fine cuts
-
-
Medium hardness and abrasiveness
Medium-reinforced concrete, paving stones, curbs, clinker bricks.
Optimal universal models:-
Technic Advanced
-
XXL
-
Rapid Pro
-
-
High hardness / low abrasiveness
Granite, gabbro, porcelain stoneware, reinforced concrete, jasper, quartz, sapphire.
Specialized blades required:-
Gres Master, Elite Max, Gabbro, Duplex, Maestro – for stone and granite
-
Meteor, Extra, Classic, Super Max – for reinforced concrete
-
Metals
Cutting metal significantly increases temperature. Diamond doesn’t cut but melts the material.
Special blades are used:
-
Pro Rex
-
Metal Cut
As we can see, almost any material can be processed if the correct blade is selected — avoiding the need for heavy and expensive machines.
Important:
Most AG work is performed dry, without water. This leads to heavy dust generation — especially indoors.
Clean cut without dust: Mechanic's solution
Construction dust harms health and can ruin the final finish. Cutting concrete or brick indoors without dust extraction almost always ends in disaster.
Mechanic offers a solution — a wide range of accessories for dry cutting, grinding, and drilling with efficient dust collection.
Work cleanly — choose Mechanic attachments for AGs and other tools to protect the air and the result.
Advantages of Distar diamond tools
Distar is not just production — it's a technological laboratory focused on practical results. The company:
-
constantly tests new materials
-
updates product lines according to construction market demands
-
considers feedback from professionals and craftsmen
-
offers solutions for specific tasks
-
uses quality materials and modern equipment
The result — reliable, accurate, and durable diamond blades proven in real-world conditions.
Conclusion
Working with an angle grinder and diamond blades gives you a universal tool that can replace an entire fleet of machines.
Successful cutting is impossible without a properly selected blade and grinder.
Distar offers solutions for any case — from budget to premium, from universal to highly specialized.
Choose wisely — and any material will yield on the first cut.