Diamond Blade – What Is It?
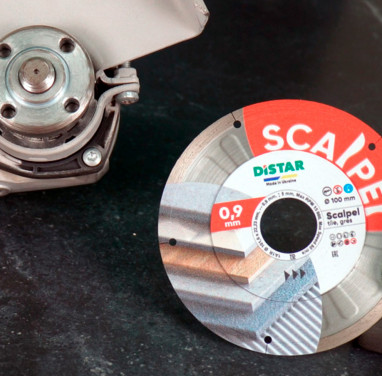
When people first hear the term diamond blade, they often imagine a tool made from rare natural diamond. However, this assumption does not fully reflect reality. Let's take a closer look at the construction of a diamond blade, as it is a fascinating and intriguing topic.
What Does a Diamond Blade Look Like?
Most readers have likely encountered diamond tools at some point, but if you have never seen a diamond blade, you might be surprised to learn that it doesn’t sparkle like a gemstone. Instead, it is a simple steel disc with tiny synthetic diamond particles embedded along its edge.
Depending on the type of equipment they are designed for, diamond blades come in a wide range of sizes—from small ones, as compact as a coin pocket in your wallet (starting from 50 mm), to massive blades taller than a person (up to 3000 mm).
On the steel core of the blades, you can find a label or UV-printed marking that provides valuable information, such as:
- Blade diameter and mounting hole size
- Type of material the blade is designed for
- Pictograms indicating compatible equipment
- Pictograms specifying the operating mode (dry or wet cutting)
- Maximum permissible rotational speed
- Blade rotation direction
Now that you know what a diamond blade looks like, let's answer the question: What is a diamond blade made of?
Diamond Blade Construction
Diamond blades consist of several key components, each with specific physical properties and varying levels of hardness. This allows manufacturers to tailor the cutting characteristics of the blade to suit different building materials.
Synthetic Diamond
Diamond is one of the hardest naturally occurring minerals, capable of cutting almost any construction material. However, diamond tools are made exclusively with synthetic diamonds, as they are significantly cheaper than natural ones. Through the synthesis process, manufacturers have been able to produce diamonds with exceptionally high hardness, nearly matching that of natural diamonds in terms of durability.
Different blades contain synthetic diamonds of varying hardness to optimize performance for specific materials. In addition to hardness, the diamond coating plays a crucial role in increasing wear resistance and enhancing the bond between the diamond particles and the cutting segment of the blade.
Diamonds can either be uncoated or covered with a thin layer of metals such as titanium, nickel, or others. Coated diamonds have increased wear resistance and remain securely embedded in the cutting edge even under high loads and overheating conditions.
Blade Core
The core of the blade is a steel disc, which may be either solid or segmented. It has a central mounting hole, whose size depends on the type of equipment the blade is designed for, such as:
- Angle grinders
- Tile cutters
- Stone saws
- Concrete cutters
- Wall saws, etc.
The diameter of the mounting hole is also adapted to the equipment type. For example, diamond blades for angle grinders commonly have a 22.23 mm hole to fit the standard clamping flange.
However, the most crucial aspect of the core is the quality of the steel used. Some blades, designed for cutting soft and abrasive materials, may be made from softer, more affordable steel. Meanwhile, blades used for cutting harder materials such as reinforced concrete require more durable and sometimes hardened steel.
Another important factor is blade thickness. The thicker the core, the more powerful the machine must be to perform the cut. Blade thickness also affects cutting precision. For example, when cutting ceramic tiles or porcelain, professionals often choose thin blades (no thicker than 1 mm) because they provide clean and precise cuts. In contrast, thicker blades are used for concrete cutting, as they can withstand high loads and extreme temperatures.
Metal Powder Bonding
With a steel core and synthetic diamond in place, the next challenge is: How are diamonds securely attached to the blade?
In most cases, this is achieved through powder metallurgy. The diamonds are mixed with various metal powders (e.g., iron, copper, bronze, tin, nickel, chromium, tungsten, cobalt, etc.), then pressed and sintered onto the steel core at high temperatures (above 800°C), sometimes under additional pressure.
The choice of metal powders influences the hardness of the diamond segment, which is a crucial factor when cutting materials with different hardness and abrasiveness levels.
Besides powder sintering, there are alternative technologies for embedding diamonds onto the blade—such as vacuum brazing and electroplating. However, tools made using these methods have a much shorter lifespan than sintered diamond blades. This is because vacuum-brazed and electroplated blades have only one layer of diamonds, while sintered blades can have multiple layers, increasing their durability.