Bridge type electric tile cutter. Selection, configuration, problems and solutions.
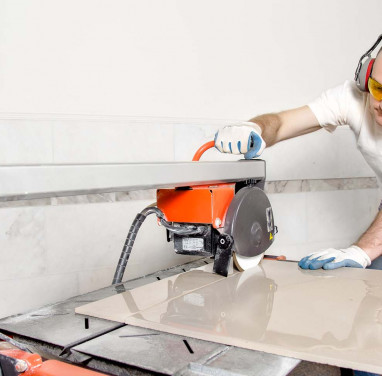
Very often after purchasing a tile cutter and cutting tiles with it, the tiler encounters problems, such as significant chipping, non-parallel or curved cut, significantly drops cut speed, and others.
These problems are caused by a lot of factors. The biggest one is connected with the design features and the adjustment of the tile cutter. The smaller part of them is related to the diamond blade.
In this article we will tell you which tool on the market, has structural advantages, how to properly configure and maintain the tile cutter and much more.
The main factors to pay attention, choosing a machine.
What factors should be paid attention to when selecting this type of equipment?
It's recommended to choose a new tile cutter responsibly: there are many models of different manufacturers and quality characteristics on the market.
The right chosen tile cutter will allow you to carry out quality work, as well as minimize time and maintenance costs.
Power of the electric motor. This is a significant parameter, as it directly affects the cutting process of hard materials and, foremost, thicker gres. The more powerful the electric motor of the tile cutter is, the greater the range of materials and the faster to be cut.
The design of the boom on which the carriage moves. There are 2 types of booms on the market, on which the carriage moves.
1. U-shaped section.
The main problem of machines with this type of boom is the bearings. They can become rusty in a humid environment, sludge and larger particles can get into them, which can quickly make them unusable.
Broken and rusted bearings make it difficult for the carriage to move and affect the straightness of the cut. If you have already purchased such a machine, it is recommended to change the bearings periodically (1-2 times a year).
In addition, the carriage makes a small groove as it moves along the boom, and creates a backlash. This backlash must be eliminated by tightening the eccentrics on which the bearings are located.
2. X-shaped boom.
In this design, there are no bearings, and special rollers move on the guide rail. This design is more reliable and lasts much longer without maintenance.
Perpendicularity to the material and straightness of the cut is maintained throughout the entire service life. Backlashes can be easily removed thanks to stopping screws, that press the rollers to the boom.
Before you buy a machine, try to find reviews, testimonials, and recommendations for configuration and maintainability on the Internet. Perhaps after viewing such information, you will make a decision about buying a different model of machine!
Water supply.
Many machines have a one-way water supply to the diamond blade. During operation, the water flows unevenly into the cutting zone. This is fraught with a decrease in the cutting ability of the diamond blade, the appearance of curvature in cutting, increased chipping on the blade's side, where there is no water supply.
It is better to give preference to a design with a double-sided water supply.
Another important aspect is the power of the water pump. The water must be abundantly supplied to the cutting area; otherwise, the supply will be minimal and this can also lead to grinding down of the diamonds.
If you have already purchased a tile cutter and found that the pump is not powerful enough - you can pick up and buy another one. There are many of their models on the market with flow rates ranging from a few liters per minute to several tens of liters per minute.
For our purposes, a pump with a water flow rate of 8-15 liters per minute will do. It is significant to have a good pump when cutting at a 45-degree angle. Since most machines make this cut by tilting the boom and carriage, the pump must provide a good water supply in this position as well.
The material from which the table and the coolant tank are made. In constant contact with water, metal rusts very quickly. The machine loses its marketable good look, and corrosion leads to holes in the coolant tank.
A machine made of aluminum materials has high corrosion resistance. In addition, some manufacturers have begun to resort to making small plastic water containers instead of bulky metal trays. They are much easier to clean and do not corrode.
The diameter of the supporting and clamping flanges. Often, the flanges on tile cutters, come in diameters from 60 to 100 mm. This parameter is rarely specified by the manufacturer, so it should be clarified additionally.
Flanges directly affect the rigidity of the blade, so if the flanges are small - it is better to use a thicker blade, and vice versa, on large flanges, thinner blades are mainly used so that the rigidity is not excessive.
Most manufacturers of consumables for tile cutters try to produce thin blades, so it is better to have a tile cutter with flanges of maximum diameter.
These are the most basic parameters that affect both the quality of tile processing and the speed of the work performed.
Based on this, it becomes clear that the most suitable for the processing of the tile is a powerful tile cutter with an X-shaped section of the boom, a water pump of medium power and large flanges. Exactly this kind of equipment will be very easy to maintain and provide a quality cut.
Adjusting tile cutters.
Whether the machine is new or worked for more than a year, it requires periodic adjustment and checking of the parallelism and perpendicularity of components, especially if the straightness of cutting is lost.
In most cases, the necessary adjustments can be made on your own, if you have a tool.
Adjustment carriage and its movement. If the tile cutter has already been used, the first thing to do is to check the carriage for backlashes and perpendicularity of the blade to the table.
All backlashes should be removed, and the carriage must move freely and smoothly along the boom, without applying excessive force. All this is adjusted by eccentrics with bearings.
The bearings also should be checked for suitability and replaced if they are corroded, and you can hear a knocking sound inside them. On all tile cutters, the bearings are removed using pullers. After this adjustment, it is worth installing the diamond blade to check perpendicularity to the table with a square.
The angle of 90 degrees must be strictly observed; otherwise, it's necessary to reconfigure the eccentrics.
Perpendicularity of the blade to the stop plank. All tile cutters are equipped with a special plank in which the tile is resting, and thus a straight cut is obtained. Often it comes with a marking, the so-called ruler.
This plank is not always set correctly, and the angle of 90 degrees with respect to the blade may not be observed. It is easy to check this with square and adjust this plank, if possible.
On some machines it's not adjustable, then you should not lean on it to make straight cuts.
Adjusting the water cooling. We have already mentioned, that this is a significant factor that can directly affect both: the quality of the edge and the performance of the blade as a whole.
If it so happens that you have a tile cutter with a one-sided water supply, it's better to remake it yourself to a two-sided water supply relative to the blade. To do this, it's enough to buy a water splitter (see figure) and a couple of short hoses of the required diameter.
Most likely, if the water supply was made to one side, the pump is low-powered. For a double-sided supply, it's advisable to replace it with a more productive model. Such an upgrade will be budgetary, but it will significantly improve the operating conditions of the diamond blade.
Check for backlash in the mounting area. This defect can be detected when installing the blade. After installation, it should sit firmly on the support flange, without being able to shift from the axis.
If there is a backlash, it is very likely that radial runout is present in the cut, which can cause chips. Another problem is, that it may lead to uneven wear of the blade and its premature failure. If such backlash appears on the supporting flange, it is necessary to replace it.
After these steps, the tile cutter is set up and ready to work.
Tile cutting technique.
Tilers are using several methods to cut the material. Some methods are more labor-intensive, but as the result you get a quality and straight cut, even on a relatively budget-friendly machine.
Frontal cut at point-blank range. The most common method is to lay the tile close to the stop plank and make the cut.
To use this method, we must be sure that the stop plank gives a clear perpendicularity of the tile in relation to the blade.
Often, in this method of cutting, the tile is not clamped to the table, just simply pressed down by hand. This cut is mainly used for cutting at 90 degrees.
Frontal cut without stop. It is used if the stop does not provide a perpendicular. After marking, the material is either clamped rigidly to the table with clamps or held by a cutter.
With this method, both 90 and 45 degrees can be cut. While cutting, the cutter can move the tile smoothly, so as not to damage the diamond blade or the material being cut.
Pendulum cut. Can be used with or without a stop. To make this cut, you must have a tile cutter with adjustable depth of cut.
The blade is positioned in that position, that cuts through a few mm of material, and the cut is made in several passes. Each subsequent approach is performed with a greater depth.
This is done to reduce the load on the electric drive and to ensure high straightness of cut when machining very hard porcelain gres. It is only used for cutting at 90 degrees.
Feeding the ceramic tiles on the blade. This method is more suitable for miter cut. The head of the tile cutter is fixed in one position, and the tiles are manually fed onto the blade.
It is worth considering, that the table must be slippable to move the tiles smoothly. With this cutting technique, you can make short cuts at 45 degrees even if your tile cutter is not configured and the bearings are broken.
Depending on your equipment, material and tasks, it's up to you which method is best to use. If you have a properly configured machine, and you can't get a clean edge or a straight cut with different cutting techniques, then the problem may be with the diamond blade.
The blade makes large chips or leads away. Start cuts and sharpening.
When cutting tiles, masters face several main types of problems: significant chips, unstraight cut, blunted blade, and a drop in speed.
In 99% of these cases, the problems are solvable and there are several ways to improve the cut quality. Let's look at these main problems, why they can occur, and how to get rid of them.
High chips. Sometimes you can get rid of this problem at the stage of buying a diamond blade. How to choose the proper blade for a particular task, you can read in the article “Cutting gres on tile cutters”.
If you have purchased a new blade, which should give a clean cut - you need to start using it correctly. Installing the blade, sometimes it's tight on the spindle of the machine. In this case, you should never use excessive force to “shove” it in, because you can deform the body.
This happens due most manufacturers do not remove the paint from the blade bore. You can do this with a knife, file or sandpaper. After a new blade was installed, make a few start cuts, due to the diamond edges being very sharp. Make a few start cuts in the tile waste to blunt a bit the diamond's edge.
The optimal starting cuts are 3 to 5 linear meters of material cut through. If the bedded blade still gives large chips, the possible reason for this is insufficient rigidity of the body.
Try cutting material with a pendulum method to reduce the load on the body. Chipping can also be caused by run-out of the blade or flanges. Make sure that the surface of the flanges adjacent to the surface of the diamond blade body is clean.
But even these manipulations do not guarantee a 100% clean cut, because there are very sharp, glossy or other types of surfaces. To finish such edges, abrasive blades or bar TM “Baumesser” are used.
No straightness of the cut. The main reasons for this defect are that the machine is not configured correctly, or that the blade is not rigid enough. If you check that your tile cutter is configured correctly, the problem is insufficient rigidity of the blade, and you can check this with a pendulum cut.
If using the pendulum method you get a straight cut, then the blade body is not rigid enough. Those you need a thicker blade or the "Hard Ceramics Advanced" by TM DISTAR. This blade has a very high cutting capacity, which significantly reduces the load on the body, eliminates its deformation.
The cutting speed has dropped, or the blade is not cutting at all. If your blade is blunt, do not try to increase the speed by applying excessive force. In that case, you may deform the body.
One of the possible causes is a large accumulation of sludge in the coolant. The water needs to be changed in time; otherwise, the sludge will constantly grind down and polished the diamonds.
Change the water and try a few more cuts. If the cutting speed has not increased, you can sharpen the diamonds of such blade with “Abrasive” bar by TM “Mechanic”. How to sharpen a blade correctly, you can see in this video:
In addition, the reason may be in a quite strong porcelain gres, for the processing of which it is better to have a “Hard Ceramics Advanced” blade.
If these manipulations did not help you to solve the problem, then you can contact the manufacturer of the diamond tool with a complaint about the quality of the purchased product!
Conclusions
In conclusion, we would like to say that a quality cut can only be achieved with a good and well tuned machine together with quality and correctly selected diamond blade.
Thanks to this article, you will be able to adjust your tile cutter yourself, maintain it properly and be smart about the choice of the blade for different tasks! Buy quality equipment and consumables, as a result, you will minimize all the problems with tile processing!