Cięcie gresu na przecinarkach do płytek
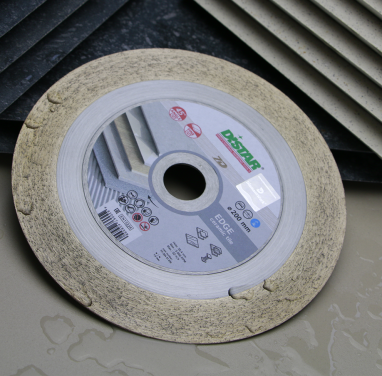
Aby stworzyć piękne wnętrze lub wystrój na zewnątrz wykorzystując płytki ceramiczne, musisz mieć nie tylko dobre doświadczenie, ale także bogaty arsenał narzędzi. Nie zawsze wszystkie niezbędne prace można wykonać za pomocą szlifierki kątowej lub ręcznej monokrystalicznej przecinarki do płytek.
I jeśli zastanawiałeś się o wykonaniu tego rodzaju pracy na elektrycznej przecinarce do płytek, ten artykuł może być bardzo przydatny. W nim rozważymy rodzaje przecinarek do płytek, ich zalety i wady, powiemy Ci, jak wybrać odpowiednią tarczę do różnych operacji i wiele innych rzeczy.
Zalety elektrycznej przecinarki do płytek w porównaniu ze szlifierką kątową.
Najczęstszym urządzeniem do cięcia płytek jest szlifierka kątowa ze względu na jej zwartość, cenę i zakres wykonywanych operacji, ale nie oznacza to, że szlifierka kątowa jest panaceum na wszelkiego rodzaju prace związane z obróbką glazury.
Elektryczne przecinarki do płytek mają również wiele zalet i umożliwiają wykonywanie takich operacji, których wykonanie na szlifierce kątowej jest albo niemożliwe, albo wymaga bardzo wysokiego poziomu profesjonalizmu. Jakie są zalety i wady przecinarki do płytek w porównaniu ze szlifierką kątową?
Sprzęt | Zalety | Wady |
---|---|---|
Przecinarka do płytek | Minimalne odpryski, wysoka prostoliniowość cięcia, brak kurzu, ergonomia (jest stół). | Cena, koszt materiałów eksploatacyjnych, brud. |
Szlifierka kątowa | Cena, zwartość, możliwość wykonywania cięć krzywoliniowych, koszt materiałów eksploatacyjnych, możliwość wykonywania dodatkowych operacji z gresem – wiercenie i bizotowanie. | Wysokie odpryski, kurz, niedostateczna prostoliniowość cięcia. |
Jak widać, trudno jest zastąpić przecinarkę do płytek takim narzędziem jak szlifierka kątowa w przypadku, gdy musimy osiągnąć minimalne odpryski na płytce i zachować maksymalną prostoliniowość cięcia.
Minimalne odpryski podczas obróbki gresu ostatnio zyskują coraz większą popularność, ponieważ staje się modny minimalizm, a wnętrza odchodzą od stosowania listew, narożników i innych elementów dekoracyjnych, dzięki którym można ukryć odpryski na płytkach, powstałe w wyniku cięcia.
Rodzaje przecinarek do płytek.
Rynek oferuje bardzo szeroką gamę urządzeń do cięcia płytek na mokro, a więc przyjrzymy się temu tematowi i zastanowimy się, jakie są przecinarki do płytek pod względem położenia wrzeciona, wymiarów stołu i średnicy stosowanych materiałów eksploatacyjnych, oraz przeanalizujemy ich główne różnice.
Zgodnie z lokalizacją wrzeciona, maszyny do cięcia na mokro są podzielone na 2 typy – górny i dolny.
Przecinarki do płytek z górnym położeniem wrzeciona. Nazywane są też typu mostowego, ponieważ podzespół tnący z tarczą porusza się po tak zwanym moście.
Maszyny te wymagają starannego ustawienia równoległości tarczy do prowadnicy, a także częstej konserwacji łożysk w celu zapewnienia wygodnego cięcia. Cięcie prostoliniowe odbywa się za pomocą przesuwania podzespołu tnącego z tarczą.
Cięcie pod kątem 45 stopni odbywa się przez przechylenie prowadnicy wraz z podzespołem tnącym i tarczą. Na nich stosuje się tarcze o średnicy 115-400 mm (najbardziej rozpowszechnione 200-250 mm).
Przecinarki do płytek z dolnych położeniem wrzeciona. Wrzeciono tego rodzaju sprzętu znajduje się pod stołem, nazywane są również maszynami zanurzeniowymi.
Są bardziej kompaktowe, mają mniej ergonomiczny stół, są mniej wydajne, niż przecinaki do płytek typu mostowego, natomiast łatwiejsze w konserwacji. Cięcie na takich maszynach odbywa się za pomocą podawania płytek na tarczę.
Cięcie pod kątem 45 stopni odbywa się za pomocą nachylenia stołu z płytkami. Jako materiał eksploatacyjny stosuje się tarcze o średnicy 200 mm -250 mm.
Biorąc pod uwagę wymiary przecinarek do płytek, można je warunkowo podzielić na 3 kategorie:
Krótkie. Rozmiar obrabianej płytki do 600 mm. Często są to maszyny o niskiej mocy (do 1 kW), zarówno zanurzeniowe, jak i mostowe. Służą do obróbki płytek o małym formacie.
Średnie. Do 1200 mm. Maszyny o takich wymiarach są produkowane tylko typu mostowego i mają moc do 1,5 kW. Dają możliwość obróbki gresów średnioformatowych o wymiarach do 1200 mm.
Długie. Powyżej 1200 mm. Takie przecinaki do płytek są również produkowane tylko w typu mostowego. Często mają silnik o mocy powyżej 2 kW. Są używane do cięcia płytek średniego formatu o wymiarach do 2 m, a nawet nieco większych.
Najczęściej stosuje się tarcze 115-125 mm o małej średnicy.
Na podstawie powyższego tekstu staje się jasne, że maszyny zanurzeniowe są używane tylko do obróbki płytek o małych wymiarach, a do pracy ze średnią potrzebna już jest mocniejsza i wymiarowa przecinarka do płytek typu mostowego.
Wykonywane operacje.
Wszystkie cięcia płytek, wykonywane na maszynach do cięcia na mokro, można z grubsza podzielić na 3 kategorie.
- Cięcie. Tutaj zaliczamy prostoliniowe cięcia, które nie wymagają idealnie czystego cięcia, ponieważ będą ukryte pod dekoracyjnymi detalami lub nie będą widoczne.
- Wykańczanie. Jeśli płytka zostanie ułożona w widocznych miejscach i nie zostanie zachowana elementami dekoracyjnymi, należy ją ciąć tak czysto, jak to możliwe, bez odprysków.
- Bizotowanie na 45 stopni. Wszystkie narożniki lub kolumny, na których układana jest płytka, wymagają jej bizotowania do dalszego dopasowania.
W zależności od niezbędnych operacji na danym obiekcie, można rozpocząć wybór diamentowej tarczy do przecinarki do płytek.
Wybór tarczy do cięcia pod kątem 90 i 45 stopni.
Niektórzy fachowcy używają jednej tarczy do wszystkich zadań, jednak jest to zasadniczo błędne podejście. Cięcie pod kątem 90 stopni i bizotowanie są zasadniczo różnymi procesami i wymagają odpowiedniego podejścia.
Nawet dla różnych rodzajów płytek, w zależności od ich grubości i struktury, pożądane jest dobranie indywidualnej tarczy. Przejrzyjmy się, która z tarcz najlepiej radzi sobie z poszczególnymi zadaniami.
Oszczędne cięcie. W tych przypadkach, gdy wykonuje się cięcie pod kątem 90 stopni, a jakość krawędzi nie jest ważna – naszym zadaniem jest maksymalne obniżenie kosztów cięcia bieżącego metra płytki, oszczędzając na materiałach eksploatacyjnych.
Do takich zadań najlepiej nadają się tarcze diamentowe TM "Baumesser” – “Hart Keramik” oraz TM "Distar” – “Ceramic Granite”. Tarcze te mają niską cenę i są bardzo dobre w obróbce płytek ceramicznych i płytek gresowych o grubości do 10 mm.
Wykończenie i oszczędne cięcie pod kątem 90 stopni. Najbardziej optymalną tarczą do wykonywania wykończeniowego cięcia prostoliniowego jest "Hard Ceramics" od TM "Distar”. Przy średniej cenie ma bardzo wysoką żywotność, co sprawia, że koszt cięcia jest niski, a jakość krawędzi jest znacznie lepsza niż w przypadku tarcz opisanych powyżej.
Bizotowanie. Proces bizotowania radykalnie różni się od cięcia pod kątem 90 stopni, ponieważ jedna część tarczy ma kontakt z 12 mm obrabianego przedmiotu, a druga z 14 mm (pod warunkiem bizotowania płytek o grubości 10 mm).
Ponieważ obciążenie jest nierównomierne, jedna strona tarczy zużywa się intensywniej, a korpus ma większe obciążenie, niż podczas normalnego cięcia. Właśnie do takich zadań została zaprojektowana tarcza "Edge" od TM "Distar”.
Ma pogrubiony korpus, który pozwala maksymalnie zachować prostoliniowość cięcia, gdy jest używana pod kątem 45 stopni. Ma również zwiększoną wysokość warstwy diamentowej w celu doszlifowania płytek podczas cięcia.
Głębokie ciężkie cięcie. Czasami do rąk rzemieślników trafiają pogrubione płytki – 14-20 mm i więcej. Obróbka takiego materiału wymaga również odpowiedniego podejścia do wyboru tarczy. Grube płytki gresowe bardzo obciążają korpus tarczy i mogą prowadzić do jego deformacji.
Do obróbki takich materiałów są idealne tarcze TM "Distar" - "Granite Premium" oraz "Hard Ceramics Advanced". Obydwie te tarcze mają segmentową warstwę diamentową i korpus. Specjalnie do obróbki ciężkich płytek gresowych optymalnie dobrany zestaw diamentów.
Granite Premium – doskonałe rozwiązanie do cięcia grubych materiałów, jeśli nie ma znaczenia jakość ciętej krawędzi, ponieważ bardzo trudno jest uzyskać z jej pomocą cięcie wykończeniowe.
Hard Ceramics Advanced natomiast stanie się lepszym wyborem do bardziej czystego cięcia grubych materiałów.
Tarcza nie tnie. Powody i sposoby wyjścia z sytuacji.
Produkcja nowoczesnych płytek gresowych nie stoi w miejscu i stale się rozwija.
Stosuje się nowe surowce oraz różne plastyfikatory i utwardzacze w celu przyspieszenia produkcji. Niestety producenci płytek nie zastanawiają się o tym, jak te lub inne pierwiastki chemiczne wpływają na ich obróbkę.
Czasami producenci narzędzi diamentowych nie mają czasu na doskonalenie składników diamentowych do obróbki płytek, a pracownicy mogą się zetknąć z tym, że tarcza przestaje ciąć. Diamenty są zatępione, tarcza jest cała w lepkim brudzie, i prędkość obróbki kilkakrotnie spada.
Jak znaleźć wyjście z takiej sytuacji, aby nie biec do sklepu po nową tarczę i zakończyć pracę tę, która jest? Często przyczyną tępienia się diamentów może być nieterminowa wymiana wody w przecinarce do płytek.
Drobne cząstki szlamu, powstałe podczas cięcia, stale trafiają na tarczę, powodując ścieranie tnącej krawędzi diamentów, dalej mieląc się na jeszcze mniejsze cząstki. Częsta zmiana wody w przecinarce do płytek znacznie wydłuży pracę narzędzia diamentowego.
Nie gwarantuje to jednak, że tarcza nie zostanie zatępiona. Drugą częstą przyczyną utraty prędkości cięcia i pojawienia się skrzywień podczas cięcia jest brak cząstek ściernych w obrabianym materiale.
Dlatego, aby naostrzyć tarczę, należy wykonać kilka cięć na wysoce ściernym materiale, na przykład na płytkach ceramicznych. Jeśli i ta metoda nie może pomóc w rozwiązaniu problemu, należy użyć specjalnej sztabki od TM "Mechanic” – “Abrasive”
Optymalnie dobrany skład wiązki ceramicznej i wielkości ziarna ściernego pozwoli skutecznie naostrzyć tarczę i kontynuować z jej pomocą pracę z wysoką wydajnością.
Jak prawidłowo naostrzyć tarczę można zobaczyć w tym wideo: